سیم و کابل مقاوم در برابر حرارت و فشار به دسته ای از محصولات الکتریکی اطلاق می شود که به طور خاص برای عملکرد قابل اعتماد در دماهای بسیار بالا و فشارهای محیطی زیاد طراحی و ساخته شده اند. عملکرد فنی این محصولات بر پایه توانایی حفظ خواص الکتریکی و مکانیکی در شرایط سخت استوار است. به عبارت دیگر این کابل ها باید قادر باشند جریان الکتریکی را به طور ایمن و بدون افت کیفیت در دماهای فراتر از محدوده های کاری سیم و کابل های معمولی منتقل کنند و در عین حال در برابر فشارهای مکانیکی و محیطی که در این دماها معمولاً وجود دارد مقاومت نشان دهند.
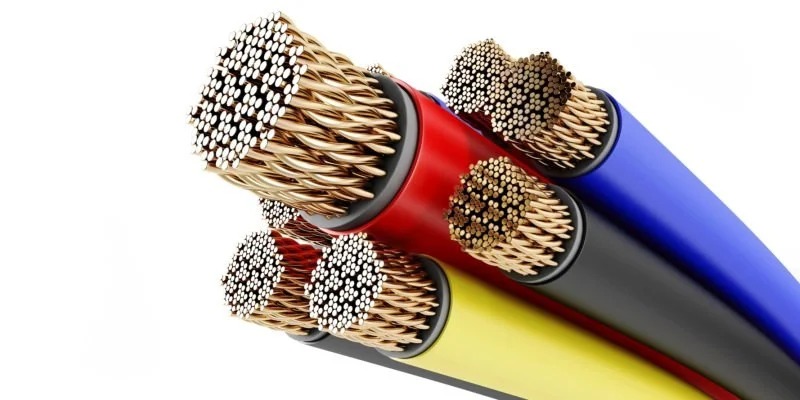
برای خرید سیم و کابل افشان از پارس تکین با کیفیت عالی در ادامه همراه ما باشید.
مقاومت در برابر حرارت و فشار یک ویژگی چندوجهی است که به عوامل مختلفی وابسته است از جمله :
- مواد سازنده : انتخاب مواد مناسب برای هادی عایق و روکش کابل اصلی ترین عامل تعیین کننده مقاومت حرارتی و فشاری است. این مواد باید در دماهای بالا خواص خود را حفظ کرده و در برابر تخریب ناشی از حرارت و فشار مقاوم باشند.
- طراحی ساختاری : طراحی کابل از جمله ضخامت لایه های عایق و روکش نوع و چینش رشته های هادی و استفاده از عناصر تقویت کننده مکانیکی نقش مهمی در تحمل فشار و حفظ یکپارچگی ساختاری کابل در شرایط سخت ایفا می کند.
- فرآیند تولید : فرآیندهای تولید پیشرفته و کنترل کیفیت دقیق اطمینان می دهند که کابل نهایی دارای خواص مطلوب و یکنواخت بوده و مطابق با استانداردهای مربوطه تولید شده است.
عملکرد فنی سیم و کابل مقاوم در برابر حرارت و فشار را می توان در دو جنبه اصلی خلاصه کرد :
- انتقال مطمئن جریان الکتریکی : در دماهای بالا مقاومت الکتریکی مواد هادی افزایش می یابد. سیم و کابل مقاوم در برابر حرارت با استفاده از هادی های با کیفیت و طراحی مناسب این افزایش مقاومت را به حداقل رسانده و انتقال جریان الکتریکی را به طور کارآمد و بدون افت ولتاژ بیش از حد تضمین می کنند.
- حفظ عایق بندی و ایمنی : حرارت و فشار می توانند باعث تخریب مواد عایق و روکش کابل شوند و منجر به اتصال کوتاه نشتی جریان و خطرات ایمنی گردند. سیم و کابل مقاوم در برابر حرارت و فشار با استفاده از مواد عایق پیشرفته و طراحی مقاوم از این خطرات جلوگیری کرده و ایمنی سیستم های الکتریکی را در محیط های سخت تضمین می کنند.
اجزای اصلی و اصول کارکرد آن
سیم و کابل مقاوم در برابر حرارت و فشار از اجزای مختلفی تشکیل شده اند که هر کدام نقش خاصی در عملکرد کلی کابل ایفا می کنند. درک اصول کارکرد این اجزا به ما کمک می کند تا اهمیت انتخاب صحیح مواد و طراحی مناسب را درک کنیم.
- هادی (Conductor) : هادی بخش اصلی کابل است که جریان الکتریکی را منتقل می کند. در سیم و کابل مقاوم در برابر حرارت و فشار معمولاً از مس با خلوص بالا یا مس با روکش نیکل استفاده می شود. مس به دلیل رسانایی الکتریکی عالی و مقاومت نسبتاً خوب در برابر حرارت گزینه اصلی است. روکش نیکل بر روی مس مقاومت به خوردگی و اکسیداسیون را در دماهای بالا افزایش می دهد به ویژه در محیط های حاوی مواد شیمیایی خورنده. در برخی کاربردهای خاص با دماهای بسیار بالا ممکن است از آلیاژهای نیکل-کروم نیز به عنوان هادی استفاده شود اگرچه رسانایی الکتریکی آن ها کمتر از مس است.
- اصل کارکرد هادی : هادی بر اساس اصل رسانایی الکتریکی عمل می کند. الکترون های آزاد موجود در ساختار فلزی هادی تحت تأثیر میدان الکتریکی ناشی از ولتاژ به حرکت در می آیند و جریان الکتریکی را ایجاد می کنند. انتخاب جنس هادی سطح مقطع و نوع تابش رشته ها (رشته ای یا مفتولی) بر میزان جریان قابل تحمل انعطاف پذیری و مقاومت کابل در برابر خستگی مکانیکی تأثیر می گذارد.
- عایق (Insulation) : عایق لایه ای است که هادی را احاطه کرده و از تماس الکتریکی بین هادی و سایر اجزای کابل یا محیط اطراف جلوگیری می کند. در سیم و کابل مقاوم در برابر حرارت و فشار از پلیمرهای مهندسی پیشرفته با مقاومت حرارتی بالا استفاده می شود. برخی از رایج ترین مواد عایق عبارتند از :
- لاستیک سیلیکون (Silicone Rubber) : لاستیک سیلیکون به دلیل انعطاف پذیری عالی مقاومت حرارتی بالا (تا حدود ۲۰۰ درجه سانتیگراد و در برخی گریدها تا ۳۰۰ درجه سانتیگراد) مقاومت خوب در برابر مواد شیمیایی و خواص دی الکتریک مناسب به طور گسترده در کابل های مقاوم در برابر حرارت استفاده می شود.
- پلی تترا فلوئورواتیلن (PTFE) یا تفلون : PTFE دارای بالاترین مقاومت حرارتی در بین پلیمرهای رایج (تا حدود ۲۶۰ درجه سانتیگراد) و مقاومت شیمیایی بسیار عالی است. این ماده در کاربردهایی که نیاز به مقاومت در برابر دماهای بسیار بالا و مواد شیمیایی خورنده وجود دارد ایده آل است.
- پرفلوروآلکوکسی آلکان (PFA) : PFA خواصی مشابه PTFE دارد اما قابلیت پردازش بهتری دارد و انعطاف پذیرتر است. مقاومت حرارتی آن کمی کمتر از PTFE است (تا حدود ۲۵۰ درجه سانتیگراد).
- پلی اتیلن متقاطع شده (XLPE) : XLPE مقاومت حرارتی بالاتری نسبت به پلی اتیلن معمولی دارد (تا حدود ۹۰ درجه سانتیگراد به طور مداوم و ۱۳۰ درجه سانتیگراد در شرایط اضطراری) و در کابل های برق با ولتاژ متوسط و بالا که نیاز به مقاومت حرارتی و عمر طولانی دارند کاربرد دارد.
- پلی آمید ایمید (PAI) : PAI مقاومت حرارتی بسیار بالایی دارد (تا حدود ۲۸۰ درجه سانتیگراد) و خواص مکانیکی و شیمیایی خوبی نیز ارائه می دهد. این ماده در کاربردهای بسیار سخت و دما بالا استفاده می شود.
- اصل کارکرد عایق : عایق بر اساس اصل مقاومت الکتریکی عمل می کند. مواد عایق تعداد الکترون های آزاد بسیار کمی دارند و در نتیجه مقاومت بسیار بالایی در برابر عبور جریان الکتریکی از خود نشان می دهند. انتخاب جنس عایق ضخامت لایه عایق و روش های عایق بندی (مانند اکستروژن نوارپیچی) بر ولتاژ قابل تحمل مقاومت عایقی و طول عمر کابل تأثیر می گذارد.
- روکش (Jacket/Sheath) : روکش لایه ی بیرونی کابل است که از عایق و هادی در برابر آسیب های مکانیکی مواد شیمیایی رطوبت اشعه UV و سایر عوامل محیطی محافظت می کند. در سیم و کابل مقاوم در برابر حرارت و فشار روکش نیز باید از موادی با مقاومت حرارتی و مکانیکی بالا ساخته شود. مواد رایج برای روکش عبارتند از :
- لاستیک سیلیکون : به دلیل مقاومت حرارتی انعطاف پذیری و مقاومت در برابر شرایط جوی لاستیک سیلیکون به عنوان روکش نیز کاربرد دارد.
- PTFE و PFA : این مواد به دلیل مقاومت شیمیایی و حرارتی عالی برای روکش کابل هایی که در معرض مواد شیمیایی خورنده و دماهای بالا قرار دارند مناسب هستند.
- پلی یورتان (Polyurethane) : پلی یورتان مقاومت سایشی و مکانیکی بسیار خوبی دارد و در کابل هایی که نیاز به مقاومت در برابر سایش و ضربه دارند استفاده می شود.
- فایبرگلاس با روکش سیلیکون : برای کاربردهای بسیار دما بالا روکش فایبرگلاس که با سیلیکون اشباع شده است مقاومت حرارتی و مکانیکی فوق العاده ای ارائه می دهد.
- اصل کارکرد روکش : روکش بر اساس اصل حفاظت فیزیکی و شیمیایی عمل می کند. مواد روکش با ایجاد یک لایه محافظ در اطراف عایق و هادی از آن ها در برابر عوامل محیطی مخرب محافظت می کنند. انتخاب جنس روکش ضخامت و نوع طراحی (مانند روکش اکسترود شده روکش بافته شده) بر مقاومت مکانیکی مقاومت شیمیایی مقاومت در برابر شرایط جوی و طول عمر کابل تأثیر می گذارد.
- شیلد (Shield/Screen) : در برخی از سیم و کابل های مقاوم در برابر حرارت و فشار به ویژه در کاربردهای حساس به نویز الکترومغناطیسی از شیلد نیز استفاده می شود. شیلد معمولاً به صورت یک لایه بافته شده از سیم های مسی یا فویل های فلزی در اطراف هادی ها یا عایق قرار می گیرد.
- اصل کارکرد شیلد : شیلد بر اساس اصل حفاظت الکترومغناطیسی عمل می کند. شیلد با ایجاد یک قفس فارادی از کابل در برابر تداخل الکترومغناطیسی (EMI) و تداخل فرکانس رادیویی (RFI) محافظت می کند. همچنین شیلد می تواند از انتشار نویز الکترومغناطیسی از کابل به محیط اطراف جلوگیری کند. شیلد باید به زمین متصل شود تا عملکرد مؤثری داشته باشد.
کاربردهای صنعتی و مثال هایی از صنایع مختلف
سیم و کابل مقاوم در برابر حرارت و فشار در صنایع مختلفی که با شرایط محیطی سخت روبرو هستند کاربردهای گسترده ای دارند. برخی از مهم ترین این صنایع و مثال هایی از کاربردها عبارتند از :
- صنایع نفت و گاز : این صنعت به طور خاص نیازمند کابل هایی است که بتوانند در دماهای بالا فشارهای زیاد و محیط های حاوی مواد شیمیایی خورنده عملکرد قابل اعتمادی داشته باشند.
- چاه های نفت و گاز (Downhole) : کابل های مورد استفاده در چاه های نفت و گاز باید در برابر دماهای بسیار بالا (تا ۲۰۰ درجه سانتیگراد و بیشتر) فشارهای شدید (هزاران PSI) و سیالات حفاری خورنده مقاوم باشند. این کابل ها برای انتقال برق سیگنال های کنترلی و داده های حسگرها در اعماق زمین استفاده می شوند. کابل های حرارتی چاه (Downhole Heat Trace Cables) نیز برای گرم کردن لوله ها و تجهیزات در چاه ها به منظور جلوگیری از تشکیل هیدرات های گازی و رسوبات پارافینی استفاده می شوند.
- پالایشگاه ها و پتروشیمی ها : در این صنایع کابل ها در معرض دماهای بالا مواد شیمیایی مختلف بخارات قابل اشتعال و محیط های انفجاری قرار دارند. کابل های مقاوم در برابر آتش (Fire Resistant Cables) و کابل های مقاوم در برابر مواد شیمیایی (Chemical Resistant Cables) برای اطمینان از عملکرد ایمن و مداوم سیستم های کنترل ابزار دقیق روشنایی و برق رسانی در این محیط ها ضروری هستند.
- صنایع هوافضا : در صنعت هوافضا وزن قابلیت اطمینان و عملکرد در شرایط دمایی و ارتفاعی شدید از اهمیت بالایی برخوردار است.
- موتورهای هواپیما و فضاپیما : کابل های مورد استفاده در موتورهای هواپیما و فضاپیما باید در برابر دماهای بسیار بالا (در نزدیکی موتور) ارتعاشات شدید و شرایط خلأ فضا مقاوم باشند. کابل های با عایق PTFE و PAI به دلیل مقاومت حرارتی و وزن کم در این کاربردها استفاده می شوند.
- اویونیک و سیستم های الکترونیکی هواپیما : کابل های اویونیک باید در برابر تغییرات دمایی شدید در ارتفاعات بالا ارتعاشات و تداخل الکترومغناطیسی مقاوم باشند. کابل های شیلددار و سبک وزن با عایق های مقاوم در برابر حرارت برای این کاربردها طراحی می شوند.
- صنایع خودروسازی : در صنعت خودروسازی به ویژه در موتور خودروها و سیستم های اگزوز کابل ها در معرض دماهای بالا روغن ها سوخت ها و سایر مواد شیمیایی قرار دارند.
- سیم کشی موتور خودرو : کابل های مورد استفاده در موتور خودرو باید در برابر حرارت موتور روغن موتور بنزین و سایر سیالات خودرو مقاوم باشند. سیم های خودرویی با عایق XLPE و روکش PVC مقاوم در برابر حرارت به طور گسترده در این کاربرد استفاده می شوند.
- سنسورهای دما و فشار : کابل های اتصال سنسورهای دما و فشار در سیستم های مدیریت موتور و سیستم های ترمز ABS باید در برابر حرارت ارتعاشات و شرایط محیطی سخت مقاوم باشند.
- نیروگاه ها : نیروگاه های حرارتی هسته ای و خورشیدی نیازمند کابل هایی هستند که بتوانند در دماهای بالا محیط های با رطوبت بالا و در برخی موارد محیط های رادیواکتیو عملکرد قابل اعتمادی داشته باشند.
- سیستم های کنترل و ابزار دقیق نیروگاه : کابل های کنترل و ابزار دقیق در نیروگاه ها باید در برابر دماهای بالا رطوبت و تداخل الکترومغناطیسی مقاوم باشند. کابل های مقاوم در برابر آتش و کابل های شیلددار برای این کاربردها استفاده می شوند.
- کابل های برق فشار قوی در نیروگاه های حرارتی : کابل های برق فشار قوی در نیروگاه های حرارتی باید در برابر دماهای بالای محیط اطراف و حرارت ناشی از جریان الکتریکی مقاوم باشند. کابل های XLPE با روکش PVC مقاوم در برابر حرارت برای این کاربردها مناسب هستند.
- محیط های رادیواکتیو در نیروگاه های هسته ای : در نیروگاه های هسته ای برخی از کابل ها در معرض تابش رادیواکتیو قرار می گیرند. کابل های مقاوم در برابر تشعشع با استفاده از مواد ویژه که در برابر تخریب ناشی از تشعشع مقاوم هستند برای این کاربردها طراحی می شوند.
- صنایع تولید فولاد و آلومینیوم : در این صنایع کابل ها در معرض دماهای بسیار بالا ناشی از کوره های ذوب و فرآیندهای تولید قرار دارند.
- کوره های القایی و قوس الکتریکی : کابل های مورد استفاده در نزدیکی کوره های ذوب باید در برابر دماهای بسیار بالا (تا ۱۰۰۰ درجه سانتیگراد و بیشتر در برخی نقاط) حرارت تابشی شدید و گرد و غبار مقاوم باشند. کابل های با روکش فایبرگلاس و سیلیکون و کابل های بافته شده با روکش فلزی (Braided Metal Sheath) برای این کاربردها استفاده می شوند.
- سیستم های خنک کننده و کنترل دما : کابل های سیستم های خنک کننده و کنترل دما در صنایع فولاد و آلومینیوم باید در برابر دماهای بالا و رطوبت مقاوم باشند.
- صنایع شیشه و سرامیک : مشابه صنایع فولاد در صنایع شیشه و سرامیک نیز کابل ها در معرض دماهای بسیار بالا ناشی از کوره های پخت و فرآیندهای تولید قرار دارند.
بررسی استانداردهای بین المللی و فناوری های پیشرفته مرتبط
استانداردهای بین المللی نقش مهمی در تضمین کیفیت ایمنی و قابلیت اطمینان سیم و کابل مقاوم در برابر حرارت و فشار ایفا می کنند. این استانداردها مشخصات فنی روش های آزمون و الزامات عملکردی را برای این نوع کابل ها تعریف می کنند. برخی از مهم ترین استانداردهای بین المللی مرتبط عبارتند از :
- IEC (کمیسیون بین المللی الکتروتکنیک) : IEC مجموعه ای جامع از استانداردها را برای سیم و کابل ارائه می دهد که بسیاری از آن ها به طور خاص به کابل های مقاوم در برابر حرارت و فشار مربوط می شوند.
- IEC ۶۰۰۹۲–۳۵۱ : این استاندارد به کابل های برق و روشنایی برای کاربردهای دریایی (کشتی ها و سکوهای نفتی) می پردازد و الزامات خاصی را برای کابل های مقاوم در برابر حرارت و آتش در این محیط های سخت مشخص می کند.
- IEC ۶۰۳۳۱ : این استاندارد روش های آزمون مقاومت در برابر آتش کابل ها را تعریف می کند. کابل هایی که مطابق با این استاندارد آزمایش می شوند باید در حین آتش سوزی به مدت زمان مشخصی (مثلاً ۳۰ دقیقه ۹۰ دقیقه یا ۱۲۰ دقیقه) به عملکرد خود ادامه دهند.
- IEC ۶۰۷۵۴ : این استاندارد به آزمون گازهای خورنده و سمی منتشر شده در هنگام سوختن کابل ها می پردازد. کابل های کم دود و بدون هالوژن (LSZH) که مطابق با این استاندارد تولید می شوند در هنگام آتش سوزی دود کمتری تولید می کنند و گازهای سمی و خورنده کمتری منتشر می کنند که ایمنی را در محیط های بسته افزایش می دهد.
- IEC ۶۰۸۱۱ : این مجموعه استاندارد روش های آزمون عمومی مواد عایق و روکش کابل های الکتریکی و نوری را مشخص می کند از جمله آزمون های مربوط به مقاومت حرارتی مقاومت مکانیکی و مقاومت شیمیایی.
- UL (آزمایشگاه های بیمه گران) : UL یک سازمان مستقل صدور گواهینامه ایمنی است که استانداردهای مربوط به ایمنی محصولات الکتریکی را تدوین و محصولات را بر اساس این استانداردها آزمایش و گواهی می کند. استانداردهای UL به طور گسترده در آمریکای شمالی و سایر نقاط جهان پذیرفته شده اند.
- UL ۷۵۸ (Appliance Wiring Material – AWM) : این استاندارد به سیم های داخلی دستگاه ها و تجهیزات الکتریکی می پردازد و انواع مختلفی از سیم های مقاوم در برابر حرارت را شامل می شود.
- UL ۱۵۸۱ (Reference Standard for Electrical Wires, Cables, and Flexible Cords) : این استاندارد مرجع برای آزمون سیم کابل و سیم های انعطاف پذیر است و روش های آزمون مختلفی را برای ارزیابی خواص الکتریکی مکانیکی و حرارتی کابل ها تعریف می کند.
- استانداردهای ملی : علاوه بر استانداردهای بین المللی بسیاری از کشورها استانداردهای ملی خود را برای سیم و کابل دارند. به عنوان مثال در ایران استانداردهای ملی ایران (ISIRI) توسط سازمان ملی استاندارد ایران تدوین می شوند. این استانداردها اغلب بر اساس استانداردهای بین المللی مانند IEC و UL هستند و ممکن است الزامات خاصی را برای شرایط و نیازهای محلی اضافه کنند.
فناوری های پیشرفته مرتبط :
- نانومواد در عایق ها و روکش ها : استفاده از نانومواد مانند نانولوله های کربنی نانوذرات سیلیکا و نانوکامپوزیت های پلیمری در مواد عایق و روکش کابل ها می تواند خواص آن ها را به طور قابل توجهی بهبود بخشد. این مواد می توانند مقاومت حرارتی مقاومت مکانیکی مقاومت شیمیایی و خواص دی الکتریک کابل ها را افزایش دهند.
- پلیمرهای با عملکرد بالا : توسعه پلیمرهای جدید با عملکرد بالا مانند پلیمرهای کریستال مایع (LCPs) و پلیمرهای مهندسی پیشرفته امکان تولید کابل های مقاوم در برابر حرارت و فشار با خواص بهبود یافته را فراهم کرده است. این پلیمرها می توانند دماهای کاری بالاتر مقاومت شیمیایی بهتر و عمر طولانی تری را ارائه دهند.
- طراحی های پیشرفته کابل : طراحی های نوآورانه کابل مانند کابل های کامپوزیتی (Composite Cables) که از ترکیب مواد مختلف برای بهینه سازی خواص استفاده می کنند و کابل های یکپارچه با حسگرها (Sensor Integrated Cables) که امکان مانیتورینگ دما فشار و سایر پارامترها را فراهم می کنند در حال توسعه هستند و کاربردهای جدیدی را در صنایع سخت باز می کنند.
چالش ها و محدودیت های فنی
با وجود پیشرفت های چشمگیر در فناوری سیم و کابل مقاوم در برابر حرارت و فشار هنوز چالش ها و محدودیت های فنی در این زمینه وجود دارد :
- تخریب مواد در دماها و فشارهای بسیار بالا : مواد عایق و روکش پلیمری حتی پیشرفته ترین آن ها در دماهای بسیار بالا (بالاتر از ۳۰۰ درجه سانتیگراد) و فشارهای شدید دچار تخریب ساختاری و کاهش خواص می شوند. یافتن مواد جدید با مقاومت حرارتی و فشاری بالاتر یک چالش مداوم در تحقیقات مواد است.
- حفظ انعطاف پذیری و یکپارچگی مکانیکی : بسیاری از مواد مقاوم در برابر حرارت و فشار ذاتاً سخت و غیرانعطاف پذیر هستند. حفظ انعطاف پذیری کابل در عین حفظ مقاومت حرارتی و فشاری یک چالش طراحی است. کابل های انعطاف پذیر برای بسیاری از کاربردها به ویژه در تجهیزات متحرک و رباتیک ضروری هستند.
- هزینه مواد و فرآیندهای تولید : مواد مقاوم در برابر حرارت و فشار معمولاً گران تر از مواد معمولی هستند. فرآیندهای تولید کابل های پیشرفته نیز ممکن است پیچیده تر و پرهزینه تر باشند. کاهش هزینه تولید کابل های مقاوم در برابر حرارت و فشار به منظور گسترش کاربرد آن ها در صنایع مختلف یک هدف مهم است.
- چالش های نصب و اتصال : نصب و اتصال سیم و کابل مقاوم در برابر حرارت و فشار در محیط های سخت می تواند دشوار باشد. اتصالات باید به طور قابل اعتماد در دماهای بالا و فشارهای زیاد عمل کنند و در برابر عوامل محیطی مقاوم باشند. توسعه روش های نصب و اتصال آسان تر و مطمئن تر یک نیاز مهم است.
- قابلیت اطمینان و طول عمر در شرایط سخت : عملکرد طولانی مدت و قابل اعتماد سیم و کابل مقاوم در برابر حرارت و فشار در شرایط سخت از اهمیت حیاتی برخوردار است. ارزیابی دقیق طول عمر کابل ها در شرایط واقعی کاربرد و توسعه روش های پیش بینی و بهبود طول عمر یک چالش مهم است.
نکات کلیدی برای بهینه سازی و بهبود عملکرد
برای بهینه سازی عملکرد و افزایش طول عمر سیم و کابل مقاوم در برابر حرارت و فشار رعایت نکات کلیدی زیر ضروری است :
- انتخاب صحیح مواد بر اساس شرایط کاربرد : مهم ترین گام انتخاب مواد مناسب برای هادی عایق و روکش کابل بر اساس حداکثر دمای کاری فشار محیطی مواد شیمیایی موجود و سایر شرایط محیطی است. مشخصات فنی کابل باید به دقت با نیازهای کاربرد مطابقت داشته باشد.
- محاسبه دقیق سایز کابل و ضریب کاهش جریان : در دماهای بالا ظرفیت جریان کابل کاهش می یابد. برای اطمینان از انتقال ایمن جریان و جلوگیری از گرم شدن بیش از حد کابل باید سایز کابل را به درستی محاسبه کرده و ضریب کاهش جریان (Derating Factor) را بر اساس دمای محیط و روش نصب اعمال کرد.
- رعایت روش های صحیح نصب و کابل کشی : نصب صحیح کابل ها از جمله رعایت فواصل مجاز استفاده از بست های مناسب جلوگیری از کشش بیش از حد کابل و محافظت از کابل در برابر آسیب های مکانیکی نقش مهمی در عملکرد و طول عمر کابل دارد.
- بازرسی و نگهداری دوره ای : بازرسی دوره ای کابل ها برای شناسایی علائم تخریب مانند ترک خوردگی روکش تغییر رنگ عایق و خوردگی اتصالات و انجام تعمیرات و تعویض های لازم به حفظ عملکرد و ایمنی سیستم های الکتریکی کمک می کند.
- استفاده از فناوری های پیشرفته : در کاربردهای خاص و حیاتی استفاده از فناوری های پیشرفته کابل مانند کابل های کامپوزیتی کابل های یکپارچه با حسگرها و کابل های با مواد نانویی می تواند عملکرد و قابلیت اطمینان سیستم را بهبود بخشد.
- مشاوره با متخصصان : در انتخاب و نصب سیم و کابل مقاوم در برابر حرارت و فشار برای کاربردهای خاص و پیچیده مشورت با متخصصان و مهندسان مجرب در زمینه کابل و سیستم های الکتریکی توصیه می شود.
نتیجه گیری علمی و تخصصی
سیم و کابل مقاوم در برابر حرارت و فشار اجزای حیاتی در زیرساخت های الکتریکی صنایع سخت هستند. انتخاب و استفاده صحیح از این کابل ها نه تنها عملکرد پایدار و ایمن سیستم های الکتریکی را در شرایط محیطی دشوار تضمین می کند بلکه از بروز خسارات مالی و جانی ناشی از خرابی تجهیزات و حوادث احتمالی جلوگیری می کند. پیشرفت های مستمر در علم مواد طراحی کابل و فناوری های تولید امکان تولید کابل های مقاوم تر با عملکرد بهتر و عمر طولانی تر را فراهم کرده است. با این حال چالش های فنی هنوز وجود دارند و تحقیقات و توسعه در این زمینه ادامه دارد. در آینده انتظار می رود که با توسعه مواد جدید و طراحی های نوآورانه سیم و کابل مقاوم در برابر حرارت و فشار نقش مهم تری در صنایع مختلف ایفا کنند و امکان بهره برداری ایمن و کارآمد از منابع انرژی و فرآیندهای صنعتی را در محیط های سخت تر فراهم آورند.
آیا شما به دنبال کسب اطلاعات بیشتر در مورد "سیم و کابل مقاوم در برابر حرارت و فشار – انتخابی برای کارهای سخت" هستید؟ با کلیک بر روی اقتصادی, کسب و کار ایرانی، به دنبال مطالب مرتبط با این موضوع هستید؟ با کلیک بر روی دسته بندی های مرتبط، محتواهای دیگری را کشف کنید. همچنین، ممکن است در این دسته بندی، سریال ها، فیلم ها، کتاب ها و مقالات مفیدی نیز برای شما قرار داشته باشند. بنابراین، همین حالا برای کشف دنیای جذاب و گسترده ی محتواهای مرتبط با "سیم و کابل مقاوم در برابر حرارت و فشار – انتخابی برای کارهای سخت"، کلیک کنید.